Maximizing Equipment Efficiency Through Packaging Machine Repair
Maximizing Equipment Efficiency Through Packaging Machine Repair
Blog Article
The Ultimate Overview to Product Packaging Machine Repair: Keep Your Operations Running Smoothly
In the realm of packaging, the effectiveness of operations hinges substantially on the dependability of equipment. Comprehending the ins and outs of product packaging maker repair service is critical for keeping optimum efficiency and lessening interruptions. Routine maintenance not only extends the life of these machines but also addresses usual concerns that can restrain efficiency. As we discover the subtleties of troubleshooting and the important decision-making procedure between repair and replacement, it comes to be clear that an aggressive technique can produce substantial advantages. What certain methods can organizations implement to guarantee their product packaging operations remain nonstop?
Importance of Routine Maintenance
Routine maintenance of product packaging machines is critical for making sure optimal performance and longevity. By carrying out a structured maintenance timetable, operators can recognize potential concerns before they intensify right into considerable troubles. This proactive technique not only reduces downtime yet also expands the lifespan of the devices, inevitably resulting in minimized operational expenses.
Normal inspections enable for the analysis of crucial elements such as sensors, belts, and seals. Resolving damage without delay prevents unforeseen failings that can disrupt production and cause pricey fixings. Additionally, routine maintenance assists make certain conformity with industry standards and policies, promoting a risk-free functioning setting.
In addition, maintenance activities such as cleaning, lubrication, and calibration considerably improve device effectiveness. Enhanced performance equates to constant product high quality, which is important for preserving customer complete satisfaction and brand credibility. A well-kept packaging device operates at optimal rates and lowers product waste, adding to general productivity.
Common Product Packaging Equipment Concerns
Product packaging devices, like any complex equipment, can run into a range of typical issues that might impede their performance and efficiency - packaging machine repair. One widespread trouble is inconsistent sealing, which can bring about item putridity and wastage if plans are not appropriately sealed. This usually results from misaligned parts or worn sealing components
One more constant problem is mechanical jams, which can occur as a result of international objects, used parts, or inappropriate positioning. Jams can cause hold-ups in production and rise downtime, ultimately influencing general productivity. In addition, electronic breakdowns, such as failure in sensing units or control systems, can lead and disrupt procedures to incorrect dimensions or erratic equipment behavior.
In addition, issues with item feed can also develop, where items might not be supplied to the packaging location consistently, triggering interruptions. Wear and tear on rollers and belts can lead to suboptimal efficiency, requiring instant focus to prevent additional damages.
Recognizing these common problems is crucial for maintaining the integrity of packaging procedures, making certain that machinery runs smoothly and effectively, which subsequently aids in meeting production targets and maintaining product high quality.
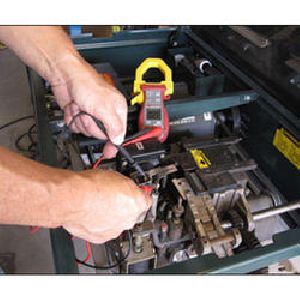
Fixing Techniques
Reliable fixing techniques are crucial for immediately attending to issues that arise with product packaging machines. An organized method is vital for recognizing the source of malfunctions and decreasing downtime. Begin by gathering details about the signs and symptoms observed; this may consist of unusual noises, functional delays, or mistake codes displayed on the maker's interface.
Next, describe the device's guidebook for troubleshooting standards specific to the design concerned. This resource can supply valuable understandings right into look at here common problems and advised diagnostic actions. Make use of visual assessments to look for loose connections, used belts, or misaligned components, as these physical elements usually add to operational failings.
Apply a process of elimination by screening specific machine functions. For instance, if a seal is not creating appropriately, assess the sealing system and temperature level setups to determine if they meet operational specs. Document each step taken and the results observed, as this can aid in future troubleshooting efforts.
Repair service vs. Replacement Decisions
When encountered with tools breakdowns, determining whether to repair or change a packaging equipment can be a facility and important option. This decision depends upon several vital variables, consisting find out here now of the age of the device, the extent of the damages, and the predicted effect on operational efficiency.
To start with, think about the device's age. Older machines might need more constant repair services, resulting in higher collective expenses that can surpass the financial investment in a new device. In addition, assess the severity of the breakdown. Minor concerns can typically be dealt with quickly and economically, whereas comprehensive damages might demand a considerable financial dedication for repairs.
Functional downtime is one more critical consideration. Investing in a new maker that offers improved performance and integrity might be a lot more sensible if fixing the machine will trigger long term hold-ups. Consider the availability of components; if replacement components are difficult to come by, it might be a lot more critical to change the machine entirely.
Ultimately, carrying out a cost-benefit analysis that includes both long-lasting and instant ramifications will certainly help in making a notified choice that lines up with your budgetary constraints and operational objectives. (packaging machine repair)
Preventative Measures for Long Life
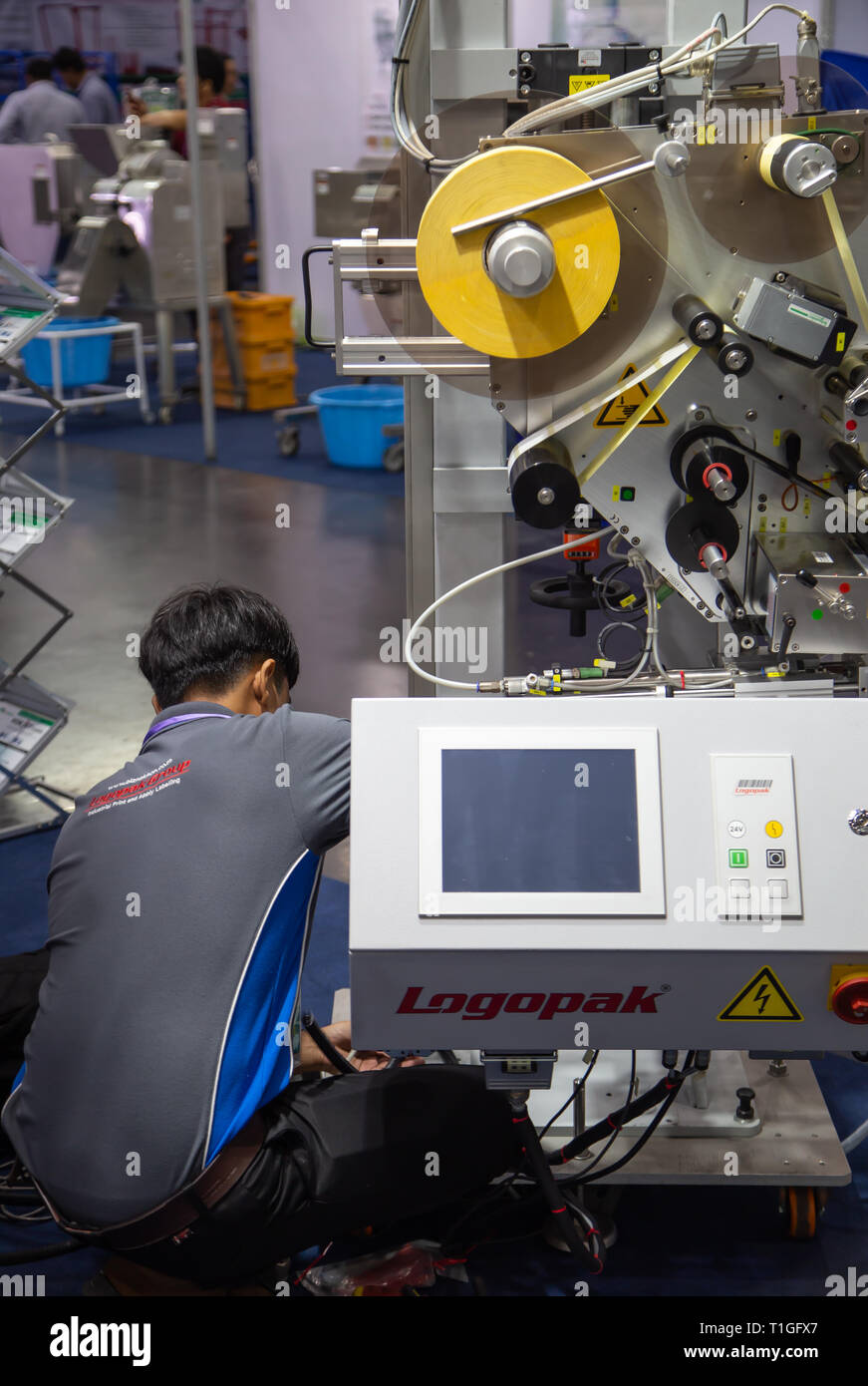
Secret precautionary actions consist of routine lubrication of moving parts, positioning checks, and calibration of sensing units and controls. Developing a cleansing timetable to remove debris and contaminants from machinery can substantially minimize damage (packaging machine repair). In addition, monitoring operational parameters such as temperature and vibration can help spot irregularities at an early stage
Training staff to recognize signs of wear or malfunction is another essential component of preventive maintenance. Empowering drivers with the expertise to execute standard troubleshooting can bring about quicker resolutions and decrease functional disturbances.
Documents of maintenance activities, including service records and evaluation findings, fosters liability and promotes educated decision-making relating to substitutes and fixings. By prioritizing safety nets, organizations can guarantee their packaging machines run at peak performance, ultimately bring about boosted productivity and reduced functional costs.
Verdict
To conclude, the effective upkeep and repair service of packaging equipments are vital for sustaining functional efficiency. Normal maintenance minimizes the danger of common problems, such as inconsistent securing and mechanical jams, while systematic troubleshooting methods facilitate punctual resolution of malfunctions. Careful factor to consider of repair versus substitute choices contributes to economical management of resources. By applying safety nets, businesses can improve equipment longevity and make sure nonstop productivity in packaging procedures.
Comprehending the ins and outs of product packaging equipment repair is essential for preserving ideal performance and lessening interruptions.Routine upkeep of product packaging makers is critical for making certain optimum efficiency and long life.Product packaging equipments, like any kind of intricate equipment, can come across a range of typical problems that may hinder their performance and performance. If fixing the maker will certainly trigger prolonged delays, spending in a brand-new maker that uses improved efficiency and reliability could be extra sensible.In final thought, the effective maintenance and fixing of packaging equipments are critical for maintaining operational efficiency.
Report this page